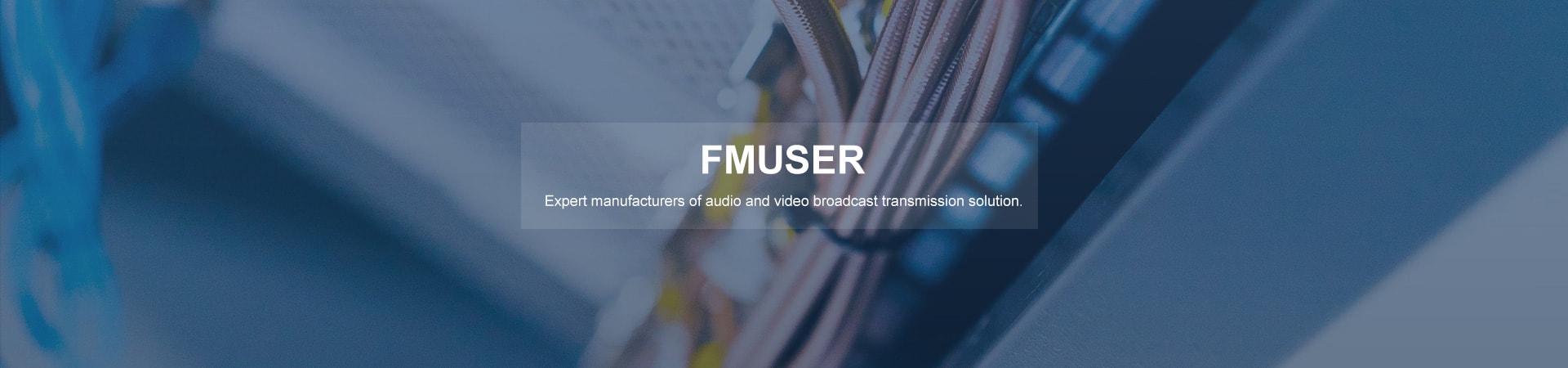
Hot tag
Popular search
A Comprehensive Guide to Fiber Optic Cable Components
Fiber optic cables have revolutionized the field of modern communication by transmitting data over long distances with incredible speed and accuracy. However, the efficiency of a fiber optic cable is not solely dependent on the cable itself, but the components used in its construction. Every part of the fiber optic cable plays a critical role in determining its speed, data security, and durability. In this article, we will delve into the different components used in fiber optic cables, including the core, cladding, buffer, coating materials, strength members, jacket materials, and more. Additionally, we will answer frequently asked questions related to fiber optic cable components.
FAQ
Here are some commonly asked questions related to fiber optic cable components.
Q: What is the purpose of the core in a fiber optic cable?
A: The core in a fiber optic cable is the central part made of glass or plastic that carries the light signal from one end of the cable to the other. The core is responsible for maintaining the signal strength and transmission speed. The diameter of the core determines the amount of light that can be transmitted, with smaller cores being better at carrying high-speed signals over long distances.
Q: What materials are used for coating fiber optic cables?
A: The coating material used in fiber optic cables is typically made of a polymer material, such as PVC, LSZH, or acrylates. The coating is applied to the core to protect it from damage, moisture, and temperature changes. The type of coating material used depends on the specific cable design, environmental regulations, and application requirements.
Q: How do strength members work in maintaining fiber optic cable integrity?
A: Strength members in fiber optic cables help to maintain cable integrity by providing structural support and preventing the cable from stretching or breaking. They can be made of various materials, including aramid fibers, fiberglass, or steel rods. The strength members are typically laid parallel to the fiber, providing flexibility and added strength. They also help to protect the cable from crushing forces and damage caused by twisting during installation.
Q: What is the difference between PVC and LSZH jacket materials?
A: PVC (polyvinyl chloride) is a widely used jacket material that provides good mechanical protection for fiber optic cables. PVC is fire-resistant but can release toxic fumes when burned. LSZH (low smoke zero halogen) jacket materials are environmentally friendly and produce low-smoke and low-toxicity levels when exposed to fire. LSZH materials are commonly used in indoor environments, such as hospitals, data centers, and aircraft, where safety is a priority.
Q: Can fiber optic cables be spliced?
A: Yes, fiber optic cables can be spliced together to create a continuous data path along a cable route. Fusion splicing and mechanical splicing are two common methods used for splicing fiber optic cables. Fusion splicing uses heat to bond the conductive cores, while mechanical splicing uses a mechanical connector to join the fibers.
I. What Are Fiber Optic Cables?
Fiber optic cables are a type of transmission medium used to transmit data signals over long distances at high speeds. They consist of thin strands of glass or plastic, known as fiber strands, that carry pulses of light representing the data being transmitted.
1. How do Fiber Optic Cables Function?
Fiber optic cables operate on the principle of total internal reflection. When a light signal enters the fiber strand, it is trapped within the core due to the difference in refractive index between the core and the cladding layer. This ensures that the light signal travels down the fiber strand without significant loss of intensity or data corruption.
To facilitate efficient transmission, fiber optic cables use a process called modulation. This involves converting electrical signals into optical signals using a transmitter at the sending end. The optical signals are then transmitted through the fiber strands. At the receiving end, a receiver converts the optical signals back into electrical signals for processing.
Lean More: An Ultimate Guide to Fiber Optic Cables: Basics, Techniques, Practices & Tips
2. Advantages over Traditional Copper Cables
Fiber optic cables offer several advantages over traditional copper cables, making them the preferred choice in many applications:
- Greater Bandwidth: Fiber optic cables have a much higher bandwidth capacity compared to copper cables. They can transmit large amounts of data at extremely high speeds, enabling faster and more reliable communication.
- Longer Distances: Fiber optic cables can carry signals over long distances without experiencing significant signal degradation. Copper cables, on the other hand, suffer from attenuation and electromagnetic interference, limiting their range.
- Immunity to Interference: Unlike copper cables, fiber optic cables are immune to electromagnetic interference from nearby power lines, radio waves, and other sources. This ensures that the transmitted data remains intact and free from distortion.
- Lightweight and Compact: Fiber optic cables are lightweight and take up less space compared to bulky copper cables. This makes them easier to install and allows for more efficient use of infrastructure.
3. Wide Usage in Various Industries
The applications of fiber optic cables span across numerous industries, including:
- Telecommunications: Fiber optic cables form the backbone of modern telecommunications networks, carrying vast amounts of data for phone calls, internet connections, and video streaming.
- Data Centers: Fiber optic cables are used extensively in data centers to connect servers and networking equipment, enabling high-speed data transmission within the facility.
- Broadcasting and Media: Broadcasting companies rely on fiber optic cables to transmit audio and video signals for television and radio broadcasting. These cables ensure high-quality transmission without loss of data or signal degradation.
- Medical and Healthcare: Fiber optic cables play a crucial role in medical imaging and diagnostic procedures, such as endoscopy and fiber optic sensors. They provide clear imaging and real-time data transmission for enhanced medical procedures.
- Industrial and Manufacturing: Fiber optic cables are employed in industrial automation and control systems, connecting various sensors, devices, and machinery. They provide reliable and high-speed communication for efficient manufacturing processes.
In summary, fiber optic cables are a critical component of modern communication systems. Their unique characteristics, such as high bandwidth, long-distance transmission capabilities, and immunity to interference, have made them the preferred choice over traditional copper cables in various industries.
II. Components of Fiber Optic Cables
Fiber optic cables comprise several key components that work together to ensure efficient and reliable transmission of data signals.
1. Fiber Strands
The fiber strands form the core component of fiber optic cables. They are typically made of high-quality glass or plastic materials that have excellent light transmission properties. The importance of fiber strands lies in their ability to carry data signals in the form of pulses of light. The clarity and purity of the glass or plastic used in the fiber strands directly impact the quality and integrity of the transmitted signals. Manufacturers carefully engineer these strands to minimize signal loss and maintain signal strength over long distances.
2. Cladding
Surrounding the fiber strands is the cladding layer, which plays a crucial role in maintaining signal integrity within the cable. The cladding is made of a material with a lower refractive index than the core of the fiber strand. This difference in refractive indices ensures that light signals transmitted through the core are contained within the fiber strands through total internal reflection. By preventing the escape of light signals, the cladding helps to minimize signal loss and improve the efficiency of data transmission.
3. Coating
To protect the delicate fiber strands from damage and environmental factors, a protective coating is applied. The coating, usually made of a durable polymer material, acts as a barrier against moisture, dust, and physical stress. It prevents the fiber strands from being easily bent or broken, ensuring the longevity and reliability of the cable. Additionally, the coating helps to maintain the optical properties of the fiber strands, preventing any interference or degradation of the signal during transmission.
4. Strength Members
To provide mechanical strength and protect the delicate fiber strands, fiber optic cables are reinforced with strength members. These strength members are typically made of aramid fibers (e.g., Kevlar) or fiberglass, which are strong and resistant to stretching. They are strategically placed within the cable to provide support and protect against tension, bending, and other physical stresses. The strength members ensure that the fiber strands are kept in alignment and remain intact, maintaining the overall structural integrity of the cable.
5. Sheath or Jacket
The outer layer of the fiber optic cable is known as the sheath or jacket. This layer serves as an additional protective barrier against external factors such as moisture, chemicals, and temperature variations. The sheath is typically made of a thermoplastic material that is resistant to abrasion and damage. It provides insulation and mechanical protection to the internal components of the cable, enhancing its durability and resistance to environmental stress.
6. Connectors
Fiber optic cables are often connected to other cables, devices, or equipment using connectors. These connectors play a crucial role in ensuring a secure and reliable connection between fiber optic cables. They allow for the easy and efficient joining and disconnection of cables, facilitating network expansion, maintenance, and repairs. Connectors come in various types, such as LC, SC, and ST, each offering different features and advantages depending on the specific application. >>View More
Working Principle of Fiber Optic Cable Components
All the components of a fiber optic cable work together to transmit light signals from one end of the cable to another. The light signal is launched into the core at one end of the cable, where it travels down the cable through a process called total internal reflection. The cladding guides and reflects the light back into the core, which helps to maintain the direction of the light signal. The coating and buffer layers provide additional protection to the glass fiber, while the strength members ensure the cable remains stable throughout its use. The jacket protects the cable from external damage and ensures that the cable remains functional.
Fiber optic cables consist of multiple components that work in harmony to enable the efficient transmission of data signals. The fiber strands carry the data signals, while the cladding maintains their integrity. The protective coating prevents damage to the fiber strands, and the strength members provide mechanical support. The sheath or jacket acts as an outer layer of protection, and connectors allow for easy connection and disconnection of cables. Together, these components make fiber optic cables a reliable and high-performance transmission medium.
Understanding the components of a fiber optic cable is crucial to comprehend how fiber optics work, their benefits, and applications. Fiber optic cables allow for faster, more reliable, and efficient transmission of data over long distances. By using fiber optic cables, people can transmit vast amounts of data over vast distances with minimal signal loss and interference.
Read Also: The Ultimate Guide to Choosing Fiber Optic Cables: Best Practices & Tips
III. Comparison of Components in Main Fiber Optic Cables Types
The market offers a range of fiber optic cables, each designed to meet specific requirements and applications. Let's explore some of the key differences in components, structure, and performance among the different types.
1. Single-Mode Fiber (SMF)
Single-mode fiber is designed for long-distance transmission and is widely used in telecommunications and long-haul applications. It has a small core diameter, typically around 9 microns, which allows for the transmission of a single mode of light. SMF offers high bandwidth and low signal attenuation, making it suitable for applications that demand long-distance, high-speed data transmission. Its compact structure enables efficient signal propagation and minimizes dispersion, ensuring clear and reliable signal transmission. >>View More
2. Multimode Fiber (MMF)
Multimode fiber is commonly used in shorter-distance applications such as local area networks (LANs) and data centers. It has a larger core diameter, typically ranging from 50 to 62.5 microns, allowing multiple modes of light to propagate simultaneously. MMF offers cost-effective solutions for shorter distances, as the larger core diameter enables easier coupling of light sources and connectors. However, due to modal dispersion, which causes signal distortion, the achievable transmission distance is significantly shorter compared to single-mode fiber. >>View More
Comparison of Single-Mode and Multi-Mode Fiber Optic Cables
Single-mode and multi-mode fiber optic cables are two main types of fiber optic cables, while both single-mode and multimode fibers have the same basic components, they differ in their construction, materials, and peak performance, for example, core diameter, cladding material, bandwidth, and distance limitations. Single-mode fibers offer a higher bandwidth and support for longer distance transmission, making them ideal for long-haul networks and high-speed communication applications. Multi-mode fibers offer lower bandwidth with shorter transmission distances, making them ideal for LANs, short-distance communication, and lower bandwidth applications. The table below summarizes the key differences between single-mode and multi-mode fiber optic cables.
Terms | Single-Mode Fiber | Multimode Fiber |
---|---|---|
Core Diameter | 8-10 microns | 50-62.5 microns |
Transmission Speed | Up to 100 Gbps | Up to 10 Gbps |
Distance Limitation | Up to 10 km | Up to 2 km |
Cladding Material | High-purity glass | Glass or plastic |
Applications | Long-haul networks, high-speed communication | LAN, short-distance communication, lower bandwidth applications |
3. Plastic Optical Fiber (POF)
Plastic optical fiber, as the name suggests, employs a plastic core instead of glass. POF is primarily used in applications that require low-cost, short-range communication. It offers relatively larger core diameters, typically around 1 millimeter, making it easier to handle and work with compared to glass fibers. While POF has higher attenuation and limited bandwidth compared to glass fibers, it offers advantages in terms of flexibility, ease of installation, and resistance to bending, making it suitable for certain industrial and automotive applications.
To help visualize the differences in components across different fiber optic cables, refer to the following table:
Component | Single-Mode Fiber | Multimode Fiber | Plastic Optical Fiber (POF) |
---|---|---|---|
Core Size | Small (around 9 microns) | Larger (50-62.5 microns) | Larger (1 millimeter) |
Cladding Type | High-purity glass | Glass or plastic | No cladding |
Coating Material | Polymer (acrylate/polyimide) | Polymer (acrylate/polyimide) | Polymer (varies) |
Strength Members | Aramid fibers or fiberglass | Aramid fibers or fiberglass | Optional |
Jacket Material | Thermoplastic (PVC/PE) | Thermoplastic (PVC/PE) | Thermoplastic (varies) |
Connectors |
Various options available |
Various options available |
Various options available |
This table provides a concise comparison of the core size, cladding type, coating material, presence of strength members, and jacket material across different types of fiber optic cables. Understanding these differences is essential for selecting the most suitable cable for specific applications and ensuring optimal performance.
You May Like: A Comprehensive List to Fiber Optic Cable Terminology
III. Comparison of Components in Speciaty Fiber Optic Cables
1. Bow-Type Drop Cables
Bow-Type Drop Cables are a type of specialty fiber optic cable designed specifically for outdoor drop applications, often used in fiber-to-the-home (FTTH) networks. These cables are known for their flat, ribbon-like structure, which allows for easy installation and termination in aerial or underground installations. Bow-Type Drop Cables offer several subtypes, each tailored to specific installation requirements.
Self-supporting Bow-Type Drop Cable (GJYXFCH)
The Self-supporting Bow-Type Drop Cable, also known as GJYXFCH, is designed for aerial installations without requiring additional support wires. This cable is ideal for outdoor use, offering excellent mechanical and environmental performance. It features a flat ribbon structure and can withstand challenging weather conditions. The absence of strength members reduces weight and simplifies installation.
Bow-Type Drop Cable (GJXFH)
The Bow-Type Drop Cable, or GJXFH, is suitable for both indoor and outdoor installations where additional support is not required. This cable offers flexibility and ease of installation, making it an efficient solution for various drop applications. The flat ribbon structure and lightweight design enable convenient handling and termination.
Strength Bow-Type Drop Cable (GJXFA)
The Strength Bow-Type Drop Cable, identified as GJXFA, incorporates additional strength members to enhance mechanical protection. These strength members, typically made of aramid fibers or fiberglass, provide extra durability and resistance against external stressors. This cable is suitable for challenging installations, including ducts or harsh environments where added strength is necessary.
Bow-Type Drop Cable for Duct (GJYXFHS)
The Bow-Type Drop Cable for Duct, sometimes referred to as GJYXFHS, is specifically designed for installation in ducts. It offers excellent performance in underground applications. This cable is typically deployed in conduit systems, providing protection and ensuring efficient fiber routing. It offers high-fiber count options, enabling increased capacity in duct installations.
Cable Comparison and Key Components
To help understand the differences and features of each Bow-Type Drop Cable subtype, consider the following comparison:
Cable Type | Fiber Strands | Ribbon Structure | Strength Members | Cladding | Coating | Connector |
---|---|---|---|---|---|---|
Self-supporting Bow-Type Drop Cable (GJYXFCH) | Varies | Ribbon | None or optional | High-purity glass | Acrylate or Polyimide | SC, LC, or GPX |
Bow-Type Drop Cable (GJXFH) | Varies | Ribbon | None | Glass or Plastic | Acrylate or Polyimide | SC, LC, or GPX |
Strength Bow-Type Drop Cable (GJXFA) | Varies | Ribbon | Aramid fibers or fiberglass | Glass or Plastic | Acrylate or Polyimide | SC, LC, or GPX |
Bow-Type Drop Cable for Duct (GJYXFHS) | Varies | Ribbon | None or optional | Glass or Plastic | Acrylate or Polyimide | SC, LC, or GPX |
These Bow-Type Drop Cables share common characteristics such as a flat ribbon structure and ease of termination. However, each cable type has unique advantages, usage scenarios, and key components.
Remember to consider these key components, advantages, and usage scenarios when selecting the appropriate Bow-Type Drop Cable for your FTTH or outdoor drop applications.
You May Like: Demystifying Fiber Optic Cable Standards: A Comprehensive Guide
2. Armored Fiber Cables
Armored fiber cables are designed to provide enhanced protection and durability in challenging environments. They feature additional layers of armor to safeguard the delicate fiber strands. Let's explore some specific types of armored fiber cables and compare their key components:
Unitube Light-armored Cable (GYXS/GYXTW)
The Unitube Light-armored Cable, also known as GYXS/GYXTW, features a single tube design with a layer of corrugated steel tape armor for physical protection. It is suitable for outdoor and aerial installations, providing robust performance and resistance to environmental factors. The GYXS/GYXTW cable typically has a fiber strand count ranging from 2 to 24.
Stranded Loose Tube Non-metallic Strength Member Armored Cable (GYFTA53)
The Stranded Loose Tube Non-metallic Strength Member Armored Cable, identified as GYFTA53, incorporates non-metallic strength members, such as aramid yarns or fiberglass, for increased mechanical reinforcement. It includes a layer of corrugated steel tape armor, offering superior protection against external forces. This cable is commonly used in harsh outdoor environments, providing excellent resistance to moisture, water penetration, and rodent damage. The GYFTA53 cable can have a fiber strand count ranging from 2 to 288 or more.
Stranded Loose Tube Light-armored Cable (GYTS/GYTA)
The Stranded Loose Tube Light-armored Cable, labeled as GYTS/GYTA, consists of multiple loose tubes, each containing several fiber strands. It features a light armor layer made of corrugated steel tape, providing increased protection without compromising flexibility. This cable is suitable for various applications where mechanical protection is required, such as direct burial or aerial installations. The GYTS/GYTA cable commonly offers a fiber strand count ranging from 2 to 288 or higher.
Stranded Loose Tube Non-metallic Strength Member Non-Armored Cable (GYFTY)
The Stranded Loose Tube Non-metallic Strength Member Non-Armored Cable, referred to as GYFTY, incorporates non-metallic strength members for mechanical support but does not include an armor layer. It offers high fiber counts and is commonly used in indoor and outdoor installations where armor protection is not required but mechanical durability is still important. The GYFTY cable typically has a fiber strand count ranging from 2 to 288 or more.
Cable Comparison and Key Components
To understand the differences and features of each armored fiber cable subtype, consider the following comparison:
Cable Type | Fiber Strands | Tube Design | Armor Type | Strength Members | Connector |
---|---|---|---|---|---|
Unitube Light-armored Cable (GYXS/GYXTW) | 2 to 24 | Single tube | Corrugated steel tape | None or optional | SC, LC, GPX |
Stranded Loose Tube Non-metallic Strength Member Armored Cable (GYFTA53) | 2 to 288 or more | Stranded loose tube | Corrugated steel tape | Aramid yarns or fiberglass | SC, LC, GPX |
Stranded Loose Tube Light-armored Cable (GYTS/GYTA) | 2 to 288 or more | Stranded loose tube | Corrugated steel tape | None or optional | SC, LC, GPX |
Stranded Loose Tube Non-metallic Strength Member Non-Armored Cable (GYFTY) | 2 to 288 or more | Stranded loose tube | None | Aramid yarns or fiberglass | SC, LC, GPX |
These armored fiber cables share common characteristics such as increased protection and durability. However, they differ in terms of their tube design, armor type, strength members, and connector options.
Remember to consider these key components and the specific requirements of your installation when selecting the appropriate armored fiber cable for your application.
3. Unitube Non-metallic Micro Cable
The Unitube Non-metallic Micro Cable is a type of fiber optic cable designed for various applications where small size and high-density are essential. This cable is often used in installations where space is limited or where flexibility is required. Let's explore its key components, advantages, and usage scenarios:
Key Components
The key components found in a Unitube Non-metallic Micro Cable typically include:
- Fiber Optic Cable: The fiber optic cable is the main component of the Unitube Non-metallic Micro Cable. It consists of optical fibers that carry the signals and a protective jacket that keeps the fibers safe from damage.
- Outer Jacket: The outer jacket is made of a non-metallic material, such as high-density polyethylene (HDPE). This jacket provides mechanical protection to the cable and is designed to withstand harsh environmental conditions, including exposure to UV radiation, temperature changes, and moisture.
- Strength Members: The strength members are located under the outer jacket and provide additional support to the cable. In Unitube Non-metallic Micro Cable, the strength members are usually made of aramid fiber or fiberglass and help to protect the cable against stress, strain, and deformation.
- Water-blocking Material: Unitube Non-metallic Micro Cable is often designed with a water-blocking material around the fiber optic cable. This material is designed to prevent water or moisture from entering the cable, which can cause damage to the cables.
Advantages
The Unitube Non-metallic Micro Cable offers several advantages, including:
- Small Size: Its compact design makes it suitable for installations where space is limited or where high-density fiber deployment is required.
- Flexibility: The non-metallic construction provides excellent flexibility, allowing for easy routing and installation in tight spaces.
- Protection: The unitube design offers protection against external factors, such as moisture, rodents, and mechanical stress.
- Simplified Termination: The single tube design simplifies termination and splicing processes, saving time and effort during installation.
Usage Scenarios
The Unitube Non-metallic Micro Cable is commonly used in a variety of applications, including:
- Indoor Installations: It is suitable for indoor installations, such as data centers, office buildings, and residential premises, where compact and flexible cabling solutions are required.
- FTTH Networks: The cable's small size and flexibility make it ideal for fiber-to-the-home (FTTH) networks, enabling efficient connectivity to individual premises.
- High-Density Environments: It is well-suited for installations in high-density environments, where multiple cables need to be routed within limited spaces.
The Unitube Non-metallic Micro Cable provides a compact, flexible, and reliable solution for various fiber optic applications. Consider these advantages and the specific requirements of your installation when selecting this cable for your project.
4. Figure 8 Cable (GYTC8A)
The Figure 8 Cable, also known as GYTC8A, is a type of outdoor fiber optic cable that features a unique figure-eight design. This cable is commonly used for aerial installations and can be attached to messenger wires or self-supporting in certain scenarios. Let's explore its key components, advantages, and usage scenarios:
Key Components
The key components found in a Figure 8 Cable (GYTC8A) typically include:
- Fiber Strands: This cable contains multiple fiber strands, usually ranging from 2 to 288, depending on the specific configuration and requirements.
- Figure Eight Design: The cable is designed in the shape of a figure-eight, with the fibers located in the center of the structure.
- Strength Members: It includes strength members, often made of aramid yarns or fiberglass, which provide mechanical support and enhance the cable's tensile strength.
- Outer Sheath: The cable is protected by a durable outer sheath, which shields the fibers from environmental factors like moisture, UV rays, and temperature variations.
Advantages
The Figure 8 Cable (GYTC8A) offers several advantages, including:
- Aerial Installation: Its figure-eight design makes it suitable for aerial installations, where the cable can be attached to messenger wires or self-supported between poles.
- Mechanical Strength: The presence of strength members enhances the cable's mechanical durability, allowing it to withstand tension and other external forces during installation and operation.
- Protection Against Environmental Factors: The outer sheath provides protection against moisture, UV radiation, and temperature fluctuations, ensuring long-term reliability in outdoor environments.
- Easy Installation: The cable's design facilitates convenient installation and termination processes, saving time and effort during deployment.
Usage Scenarios
The Figure 8 Cable (GYTC8A) is commonly used in various outdoor applications, including:
- Aerial Fiber Optic Networks: It is widely deployed for aerial fiber optic installations, such as over poles, between buildings, or along utility routes.
- Telecommunication Networks: The cable is suitable for long-distance communication networks, providing efficient data transmission over extended spans.
- Cable TV and Internet Distribution: It is utilized in cable TV and internet distribution networks that require reliable and high-bandwidth connectivity.
The Figure 8 Cable (GYTC8A) offers a robust and reliable solution for outdoor aerial installations. Consider these advantages and the specific requirements of your installation when selecting this cable for your project.
5. All Dielectric Self-supporting Aerial Cable (ADSS)
The All Dielectric Self-supporting Aerial Cable, commonly referred to as ADSS, is a type of fiber optic cable designed for aerial installations without the need for additional support wires or messenger cables. ADSS cables are specifically engineered to withstand the mechanical stresses and environmental conditions encountered in outdoor aerial deployments. Let's explore its key components, advantages, and usage scenarios:
Key Components
The key components found in an All Dielectric Self-supporting Aerial Cable (ADSS) typically include:
- Fiber Strands: This cable contains multiple fiber strands, usually ranging from 12 to 288 or more, depending on the specific configuration and requirements.
- Dielectric Strength Members: ADSS cables feature dielectric strength members, often made of aramid yarns or fiberglass, which provide mechanical support and enhance the cable's tensile strength without introducing conductive elements.
- Loose Tube Design: The fibers are housed in loose tubes, which protect them from external environmental factors such as moisture, dust, and UV radiation.
- Outer Sheath: The cable is protected by a durable outer sheath that provides additional protection against environmental factors like moisture, temperature variations, and mechanical stresses.
Advantages
The All Dielectric Self-supporting Aerial Cable (ADSS) offers several advantages, including:
- Self-supporting Design: ADSS cables are designed to support their weight and the tension applied during installation without the need for additional messenger wires or metallic support.
- Lightweight Construction: The use of dielectric materials makes ADSS cables lightweight, reducing the load on supporting structures and simplifying installation.
- Excellent Electrical Insulation: The absence of metallic components ensures high electrical insulation, eliminating the risk of electrical interference or power-related issues in the network.
- Resistance to Environmental Factors: The outer sheath and design of ADSS cables provide excellent protection against moisture, UV radiation, temperature variations, and other environmental elements, ensuring long-term reliability.
Usage Scenarios
The All Dielectric Self-supporting Aerial Cable (ADSS) is commonly used in various outdoor aerial applications, including:
- Power Utility Networks: ADSS cables are extensively used in power utility networks for communication and data transmission alongside power lines.
- Telecommunication Networks: They are deployed in telecommunication networks, including long-distance backbone networks, providing reliable connectivity for voice, data, and video transmissions.
- Rural and Suburban Deployments: ADSS cables are suitable for aerial installations in rural and suburban areas, offering efficient connectivity in diverse geographical regions.
The All Dielectric Self-supporting Aerial Cable (ADSS) provides a reliable and efficient solution for aerial fiber optic installations. Consider these advantages and the specific requirements of your installation when selecting this cable for your project.
Beyond the mentioned optical fibers, there are specialty fiber optic cables designed for specific purposes. These include:
- Dispersion-shifted fiber: Optimized to minimize chromatic dispersion, allowing for high-speed data transmission over long distances.
- Non-zero dispersion-shifted fiber: Designed to compensate for dispersion at specific wavelengths, ensuring efficient long-distance transmission with minimal distortion.
- Bend-insensitive fiber: Engineered to minimize signal loss and distortion even when subjected to tight bends or harsh environmental conditions.
- Armored fiber: Reinforced with additional layers, such as metal or kevlar, to provide enhanced protection against physical damage or rodent attacks, making them suitable for outdoor and harsh environments.
Dispersion-shifted Fiber
Dispersion-shifted fiber is a specialized type of optical fiber designed to minimize dispersion, which is the spreading of optical signals as they travel through the fiber. It is engineered to have its zero-dispersion wavelength shifted to a longer wavelength, typically around 1550 nm. Let's explore its key components, advantages, and usage scenarios:
Key Components
The key components found in dispersion-shifted fiber typically include:
- Core: The core is the central part of the fiber that carries the light signals. In dispersion-shifted fibers, the core is usually made of pure silica glass and is designed to have a small effective area to minimize the dispersion.
- Cladding: The cladding is a layer of silica glass that surrounds the core and helps to confine the light signals within the core. The refractive index of the cladding is lower than that of the core, which creates a boundary that reflects the light signals back into the core.
- Dispersion-Shifted Profile: The dispersion-shifted profile is a unique feature of the dispersion-shifted fibers. The profile is designed to shift the zero-dispersion wavelength of the fiber to a wavelength where the optical loss is minimized. This allows for the transmission of high-bit-rate signals over long distances without significant signal distortion.
- Coating: The coating is a protective layer that is applied over the cladding to protect the fiber from damage and to provide additional strength to the fiber. The coating is usually made of a polymer material.
Advantages
- Minimized Dispersion: Dispersion-shifted fiber minimizes chromatic dispersion, allowing for efficient transmission of optical signals over longer distances without significant pulse spreading or distortion.
- Long Transmission Distances: The reduced dispersion characteristics of dispersion-shifted fiber enable longer transmission distances, making it suitable for long-haul communication systems.
- High Data Rates: By minimizing dispersion, dispersion-shifted fiber supports high-speed data transmission and higher data rates without the need for frequent regeneration of the optical signal.
Usage Scenarios
Dispersion-shifted fiber finds applications in the following scenarios:
- Long-Haul Communication Networks: Dispersion-shifted fiber is commonly deployed in long-haul communication networks where high data rates and long transmission distances are required. It helps ensure reliable and efficient data transmission over extended spans.
- High-Capacity Networks: Applications such as internet backbones, data centers, and high-bandwidth networks can benefit from the improved performance and increased capacity provided by dispersion-shifted fiber.
Dispersion-shifted fiber plays a crucial role in enabling efficient and reliable data transmission over long distances, especially in long-haul communication networks that require high data rates. Its minimized dispersion characteristics contribute to the overall performance and capacity of fiber optic systems.
Non-zero Dispersion-shifted Fiber
Non-zero dispersion-shifted fiber (NZDSF) is a specialized type of optical fiber designed to minimize dispersion in a specific wavelength range, typically around 1550 nm, where the fiber exhibits a small but non-zero value of dispersion. This characteristic allows for optimized performance in wavelength-division multiplexing (WDM) systems. Let's explore its key characteristics, advantages, and usage scenarios:
Key Components
The key components found in Non-zero Dispersion-shifted Fiber typically include:
- Core: As with other types of optical fibers, the core is the region of the fiber where light propagates. However, the core of NZ-DSF is designed with a larger effective area than conventional fibers to reduce the effects of nonlinearities like self-phase modulation.
- Cladding: Like other types of fiber, NZ-DSF is surrounded by a cladding layer. The cladding is typically made of pure silica glass and has a slightly lower refractive index than the core, which helps to confine the light in the core.
- Graded-Index Profile: NZ-DSF has a graded-index profile in its core, which means the refractive index of the core decreases gradually from the center to the edges. This helps to minimize the effects of modal dispersion and reduces the dispersion slope of the fiber.
- Non-zero Dispersion Slope: The key feature of NZ-DSF is the non-zero dispersion slope, which means that the dispersion varies with wavelength, but the zero-dispersion wavelength is shifted away from the operating wavelength. This is in contrast to dispersion-shifted fibers, where the zero-dispersion wavelength is shifted to the operating wavelength. Non-zero dispersion slope fiber has been designed to minimize both chromatic and polarization mode dispersion, which can limit the data rate and distance that a fiber can support.
- Coating: Finally, like other types of fiber, NZ-DSF is coated with a layer of protective material, usually a polymer coating, to protect the fiber from mechanical damage and environmental effects.
Key Characteristics
- Dispersion Optimization: Non-zero dispersion-shifted fiber is designed with specifically engineered properties to minimize dispersion in a specific wavelength range, allowing for efficient transmission of multiple wavelengths without significant degradation.
- Non-zero Dispersion: Unlike other fiber types, which may have zero dispersion at a specific wavelength, NZDSF intentionally exhibits a small, non-zero value of dispersion in the targeted wavelength range.
- Wavelength Range: The dispersion characteristics of NZDSF are optimized for a specific wavelength range, usually around 1550 nm, where the fiber exhibits its minimized dispersion behavior.
Advantages
- Optimized WDM Performance: NZDSF is tailored to minimize dispersion in the wavelength range used for WDM systems, enabling efficient transmission of multiple wavelengths simultaneously and maximizing the fiber's capacity for high-speed data transmission.
- Long Transmission Distances: The minimized dispersion characteristics of NZDSF allow for long-distance transmission without significant pulse spreading or distortion, ensuring reliable data transmission over extended spans.
- High Data Rates: NZDSF supports high data rates and increased transmission capacity, making it suitable for high-capacity communication systems, especially when combined with WDM technology.
Usage Scenarios
Non-zero dispersion-shifted fiber is commonly used in the following scenarios:
- Wavelength-Division Multiplexing (WDM) Systems: NZDSF is well-suited for WDM systems, where multiple wavelengths are transmitted simultaneously over a single fiber. Its optimized dispersion characteristics allow for efficient transmission and multiplexing of optical signals.
- Long-Haul Communication Networks: Non-zero dispersion-shifted fiber is deployed in long-haul communication networks to achieve high data rates and long transmission distances while maintaining reliable and efficient data transmission.
Non-zero dispersion-shifted fiber plays a crucial role in enabling high-capacity and long-distance data transmission, particularly in WDM systems. Its optimized dispersion characteristics allow for efficient multiplexing and transmission of multiple wavelengths.
Bend-insensitive Fiber
Bend-insensitive fiber, also known as bend-optimized or bend-insensitive single-mode fiber, is a type of optical fiber designed to minimize signal loss and degradation when subjected to tight bends or mechanical stresses. This fiber type is engineered to maintain efficient light transmission even in situations where traditional fibers may experience significant signal loss. Let's explore its key components, advantages, and usage scenarios:
Key Components
The key components found in bend-insensitive fiber typically include:
- Core: The core is the central region of the fiber where the light signal travels. In bend-insensitive fibers, the core is usually larger than that of conventional fibers, but still small enough to be considered a single-mode fiber. The larger core is designed to minimize the impact of bending.
- Cladding: The cladding is a layer that surrounds the core to keep the light signal confined to the core. Bend-insensitive fibers has a special design of cladding which allow to minimize the amount of distortion to the light signal that passes through the fiber when bent. The bend-insensitive cladding is usually made from a slightly different material than the core, which helps to reduce the mismatch between the two layers.
- Coating: The coating is applied over the cladding to protect the fiber from mechanical stress and environmental damage. The coating is usually made of a polymer material that is both flexible and durable.
- Refractive Index Profile: Bend-insensitive fibers also have a special refractive index profile to improve their bending performance. This can include a larger cladding diameter to reduce bending losses and a flattening of the refractive index profile to reduce modal dispersion.
Advantages
- Reduced Signal Loss: Bend-insensitive fiber minimizes signal loss and degradation even when subjected to tight bends or mechanical stresses, ensuring reliable data transmission.
- Flexibility and Improved Reliability: Bend-insensitive fiber is more flexible and resistant to macro- and micro-bending than traditional fiber types. This makes it more reliable in installations where bends or stresses are unavoidable.
- Ease of Installation: The improved bend tolerance of this fiber type simplifies installation, allowing for greater flexibility in routing and deployment. It reduces the need for excessive bend-radius requirements and reduces the risk of fiber damage during installation.
Usage Scenarios
Bend-insensitive fiber finds applications in various scenarios, including:
- FTTx Deployments: Bend-insensitive fiber is commonly used in fiber-to-the-home (FTTH) and fiber-to-the-premises (FTTP) deployments, where it offers improved performance in tight and bend-prone environments.
- Data Centers: Bend-insensitive fiber is advantageous in data centers where space optimization and efficient cable management are crucial. It allows for increased flexibility and reliable connectivity within confined spaces.
- Indoor Installations: This fiber type is suitable for indoor installations, such as office buildings or residential premises, where space constraints or tight bends may be encountered.
Bend-insensitive fiber provides a reliable and flexible solution for applications where signal loss due to bending or mechanical stresses is a concern. Its improved bend tolerance and reduced signal degradation make it well-suited for various installation scenarios, ensuring reliable data transmission.
When selecting the appropriate fiber optic cable, factors such as required transmission distance, bandwidth, cost, installation environment, and specific application requirements should be considered. It is crucial to consult with experts or manufacturers to ensure the chosen cable type aligns with the intended purpose and performance goals.
In summary, the different types of fiber optic cables vary in their core diameter, transmission characteristics, and suitability for specific applications. Understanding these differences allows for informed decision-making when choosing the most appropriate fiber optic cable for a given scenario.
Conclusion
In conclusion, the components of fiber optic cables play a vital role in enabling the transmission of data at high speeds and over long distances. The fiber strands, cladding, coating, strength members, sheath or jacket, and connectors work in harmony to ensure reliable and efficient data transmission. We have seen how the materials used in each component, such as glass or plastic for the core, protective coatings, and strength members, contribute to the performance and durability of fiber optic cables.
Furthermore, we explored different types of fiber optic cables, including single-mode fiber, multimode fiber, and plastic optical fiber, each with its unique characteristics and applications. We also addressed common questions about fiber optic cable components, such as the materials used and the variations between different manufacturers.
Understanding the components of fiber optic cables is essential for selecting the most suitable cable for specific applications and ensuring optimal performance. As technology continues to advance, fiber optic cables and their components will continue to play a critical role in driving our interconnected world forward. By staying informed about these components, we can harness the power of fiber optic cables and embrace the benefits of fast, reliable, and efficient data transmission in various industries and everyday life.
Contents
Related Articles
CONTACT US

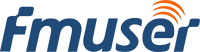
FMUSER INTERNATIONAL GROUP LIMITED.
We are always providing our customers with reliable products and considerate services.
If you would like to keep touch with us directly, please go to contact us